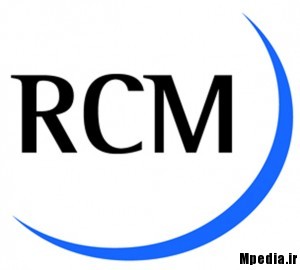
1– وظایف[1]
یک فرآیند RCM که مطابق با SAE JA 1011 باشد با این پرسش آغاز میشود که: وظایف و استانداردهای مطلوب مربوط با کارایی دارایی در زمینه عملیاتی کنونیاش چه چیزهایی میباشند؟
در این بخش به بحث درباره چهار مفهوم کلیدی زیر که مربوط به وظایف میباشند میپردازیم.
- زمینه عملیاتی
- وظایف اولیه و ثانویه
- شرح وظایف
- استانداردهای کارایی
1-1- زمینههای عملیاتی[2]
زمینههای عملیاتی دارایی باید تعریف گردند. این زمینهها عبارتاند از وظایف، مدهای خرابی، نتایج خرابی و استراتژی های مدیریت خرابی که بر هر دارایی اعمال میشوند. این امر علاوه بر اینکه به نوع دارایی فیزیکی بستگی دارد به شرایط دقیقی که دارایی تحت آن قرار دارد نیز وابسته است.
تشریح یک زمینه عملیاتی دارایی فیزیکی شامل شرح کلی مختصری از چگونگی استفاده از آن و اینکه در کجا مورد استفاده قرار می گیرد و همچنین کارایی کلی معیارهایی همچون تولید، توان عملیاتی، ایمنی، تمامیت زیست محیطی و غیره میباشد.
مسائل خاصی که باید در شرح زمینه عملیاتی مستند گردد عبارتاند از:
- فرآیندهای متناوب در مقابل فرآیندهای متوالی: دارایی فیزیکی در یک فرآیند متناوب بکار گرفته میشود یا در یک فرآیند متوالی.
- استانداردهای کیفیت: استاندارد های کیفیت شامل کیفیت کلی یا انتظارات خدمات مشتری، در قالب مسائلی مانند میزان ضایعات کلی و میزان رضایت مشتری مانند انتظار کارایی به موقع در سیستمهای انتقال، ضمانت کالاهای تولیدی و آمادگی نظامی می باشد.
- استانداردهای زیست محیطی: استانداردهای زیست محیطی سازمانی، منطقهای، ملی و بینالمللی که بر دارایی فیزیکی اعمال میشود.
- استانداردهای ایمنی: انتظارات ایمنی از پیش تعیین شدهای در قالب صدمات کلی و یا میزان تلفات که در دارایی فیزیکی بکار گرفته میشود.
- نمایش عملیاتی: ویژگیهای موقعیتی که قرار است تجهیزات در آن کار کنند. برای مثال: سردسیر و گرمسیر، بیابان و جنگل، خشکی و ساحل، مجاورت به منابع عرضه، نیروی کار و غیره.
- شدت عملیاتی: در موارد تولیدی فرآیندی که در آن تجهیزات قرار دارد میبایست 24 ساعت، هفت روز هفته یا با شدت کمتری کار کند یا خیر . در موارد خدماتی آیا تجهیزات در زمان اوج مصرف کار میکنند یا در شرایط معمولی مصرف. در موارد تجهیزات نظامی آیا استراتژی های مدیریت خرابی برای کار در زمان صلح طراحی شدهاند یا در زمان جنگ.
- جایگزین: آیا تجهیز جایگزین[3] یا آماده بکار[4] وجود دارد و در صورت وجود به چه صورت کار میکند.
- کار در زمان تولید: حدی از موجودی که به دارایی اجازه توقف میدهد بدون اینکه بر خروجی کلی یا توان عملیاتی دارایی تاثیری داشته باشد.
- یدکیها: آیا تصمیمی در خصوص ذخیره کردن یدکیهای کلیدی که ممکن است به انتخابهای بعدی استراتژی های مدیریت خرابی صدمه بزند گرفته شده است یا خیر.
- تقاضای بازار و عرضه مواد خام: آیا احتمال دارد تغییرات در تقاضای بازار یا عرضه مواد خام به انتخاب استراتژی های مدیریت خرابی بعدی صدمه بزند. چنین تغییراتی ممکن است در یک دوره یک روزه در فعالیتهای حمل و نقل شهری رخ دهد یا در دوره بیش از یک سال در مواردی چون نیروگاههای برق، شهربازی یا فعالیتهای مواد غذایی به طول انجامد.
در مواردی که سیستم بزرگ و یا پیچیده می باشد منطقی است که ساختار زمینه عملیاتی به صورت سلسله مراتبی ایجاد گردد و در صورت لزوم بیانیه ای برای استفاده از دارایی در کل سازمان توزیع گردد.
1-2- فهرست وظایف[5]
کلیه وظایف سیستم یا دارایی میبایست مشخص گردند شامل کلیه وظایف اولیه و ثانویه، مانند وظایف کلیه دستگاههای حفاظتی.
هدف فرآیند RCM توسعه یک سری استراتژی هایی می باشد که از وظایف دارایی یا سیستم با در نظر گرفتن استانداردهای کارایی که مورد پذیرش صاحبان یا استفاده کنندگان آن است، محافظت کند. در نتیجه فرآیند RCM با مشخص کردن کلیه وظایف دارایی در زمینه عملیاتی آغاز میشود.
وظایف را میتوان به دو دسته تقسیم کرد: وظایف اولیه و ثانویه.
1-2-1- وظایف اولیه: دلیل اینکه چرا یک سازمان، دارایی یا سیستمی را برای انجام یک یا چند فعالیت انتخاب میکند. این وظایف به عنوان وظایف اولیه شناخته میشوند.
برای مثال، دلیل اصلی اینکه چرا شخصی از ماشین استفاده میکند ممکن است برای ” جابجایی بیش از 5 نفر با سرعت بیش از 90 کیلومتر در ساعت در جاده باشد.”
1-2-2- وظایف ثانویه: از بیشتر داراییها انتظار میرود که علاوه بر وظایف اولیه وظایف دیگری را نیز به دنبال داشته باشند. این وظایف به عنوان وظایف ثانویه شناخته میشود. وظایف ثانویه معمولاً کمتر از وظایف اولیه قابل مشاهده است؛ اما فقدان کارکرد ثانویه نیز عواقب جدی دارد که گاهی بسیار جدیتر از نبود کارکرد اولیه است.
بنا بر آنچه که گفته شد شاید وظایف ثانویه نسبت به وظایف اولیه به توجه بیشتری نیاز نداشته باشند، ولی باید مورد توجه قرار گیرند و بنابراین آنها نیز باید به روشنی تعریف شوند. زمانی که وظایف ثانویه را تعریف میکنیم باید موارد زیر را مد نظر قرار دهیم:
- تمامیت زیست محیطی
- تمامیت ساختاری / ایمنی
- کنترل/ برخورداری/ راحتی
- ظاهر
- دستگاهها و سیستمهای حفاظتی
- اقتصاد/ کارایی
- اضافی
این مسائل با جزئیات بیشتر در زیر آورده شدهاند.
1-2-2-1- تمامیت زیست محیطی
این وظایف مشخص میکنند که تا چه حد یک دارایی میبایست با قوانین و استانداردهای زیست محیطی شرکتی، شهری، منطقهای، ملی و بینالمللی که بر دارایی اعمال میشود مطابق باشد. این استانداردها آزاد کردن مواد خطرناک در محیط زیست و اختلال در آن را کنترل میکنند.
1-2-2-2- ایمنی
گاهی لازم است شرح وظایفی که با تهدیدات خاص ایمنی مقابله میکنند و در فرایند طراحی یا کار اجتناب ناپذیر هستند را بنویسیم. برای مثال کارکرد عایق الکتریکی در یک وسیله خانگی، حفاظت استفاده کنندگان آن از جریان برق است.
1-2-2-3- تمامیت ساختاری
بسیاری از داراییها، یک کارکرد ثانویه، پشتیبان یا یک پایه محکم برای دستگاههای دیگر هستند. برای مثال هر چند کارکرد اولیه یک دیوار ممکن است محافظت از افراد و وسایل در برابر آب و هوا باشد اما پشتیبانی سقف یا تحمل وزن قفسهها و قاب عکسها نیز از آن انتظار میرود.
1-2-2-4- کنترل
در بسیاری از موارد، استفاده کنندگان نه تنها میخواهند داراییها وظایف را تا سطح استاندارد کارایی شان انجام دهند بلکه میخواهند قادر به تنظیم کارایی نیز باشند. برای مثال، کارکرد یک سیستم خنک کننده ممکن است تنظیم دما بین یک درجه دمای خاص و دمای دیگر باشد. فرم نمایش و بازخورد، زیر مجموعه مهمی از بخش کنترل رده وظایف را تشکیل میدهد.
1-2-2-5- برخورداری
سیستمهایی که کارکرد اولیه آنها ذخیره مواد است باید بتوانند آن مواد را نیز مهار کنند. به طور مشابه، سیستمهایی که مواد را انتقال میدهند به ویژه مایعات باید بتوانند آن را نیز مهار کنند. این وظایف نیز باید به روشنی مشخص شوند.
1-2-2-6- راحتی
صاحبان و استفاده کنندگان دارایی در کل انتظار دارند که داراییها یا سیستمهای آنها باعث ایجاد مشکل و اضطراب برای اپراتورها یا تعمیرکاران نشود. البته این مشکلات باید در مرحله طراحی در نظر گرفته شود. به هر حال خرابی یا تغییر انتظارات میتواند منجر به سطح غیر قابل قبولی از اضطراب و مشکل شود. بهترین راه برای اطمینان از رخ ندادن چنین مشکلی این است که مطمئن شویم توضیحات کارکرد وابسته با دقت توصیف شده و استانداردهای جاری به طور کامل در نظر گرفته شدهاند.
1-2-2-7- ظاهر
ظاهر اغلب به منزله کارکرد ثانویه مهمی می باشد. برای مثال دلیل اولیه رنگ کردن اغلب تجهیزات صنعتی حفاظت آنها از زنگ زدگی و خوردگی است. با این حال ممکن است یک رنگ روشن برای بالا بردن قابلیت دید آن به دلایل ایمنی انتخاب شود و این کارکرد نیز باید مستند شود.
1-2-2-8- حفاظت
وظایف حفاظتی از نتایج خرابی برخی وظایف دیگر جلوگیری کرده و آن را برطرف میکند یا به حداقل میرسانند. این وظایف دستگاهها و سیستمهای زیر را دارا میباشند:
- اپراتورهای هشدار شرایط غیر عادی شامل چراغها و زنگهای هشدار
- تجهیزات متوقف کننده در مواقع خرابی وظیفه ای (مکانیزم متوقف کننده)
- برطرف کننده و از بین برنده شرایط غیرعادی حاصل از خرابی وظیفه ای شامل مکانیزم آرام سازی، سیستمهای جلوگیری از حریق
- به عهده گرفتن عملیاتی که دچار خرابی شده است. (اجزای ساختاری جایگزین، منطقه آماده به کار
- جلوگیری از ایجاد شرایط خطرناک در ابتدای کار مانند علائم هشداردهنده، پوششهای حفاظتی
یک وظیفه حفاظت کننده این اطمینان را به ما میدهد که خرابی یک وظیفه بدون حفاظت بسیار جدیتر از خرابی یک وظیفه حفاظت شونده است. دستگاههای حفاظتی برای کاهش ریسک با سیستمها گنجانیده شدهاند، بنابراین وظایف آنان باید با دقت خاصی مستند شود.
1-2-2-9- اقتصاد / کارایی
در بیشتر سازمانها، انتظارات هزینه کلی به شکل بودجه مخارج بیان میشوند. با این حال برای داراییهای خاص، انتظارات هزینه ای میتواند مستقیماً از طریق تشریح وظیفه ثانویه مربوطه به عنوان میزان مصرف انرژی و میزان استهلاک مواد فرآیند نشان داده شوند.
1-2-2-10- فعالیتهای اضافی
برخی سیستمها، مولفههایی را ترکیب میکنند که اضافی به نظر میرسند. این امر معمولاً زمانی رخ میدهد که تجهیزات یا روشی که از آن استفاده میشود در طول سالها تغییر کرده باشد یا زمانی که تجهیزات جدیدی مشخص شده باشد.
البته چنین مواردی هیچ وظیفه مثبتی نداشته و اغلب برداشتن آنها هزینه بر است. این موارد در واقع ممکن است باعث ایجاد خرابی شود و در نتیجه قابلیت اطمینان کلی سیستم را کاهش دهد. به منظور جلوگیری از این اتفاقات، برخی ممکن است درخواست نگهداری و تعمیر کرده و بنابراین منابع را استفاده کنند.
اگر آنها رفع شوند، هزینهها و مدهای خرابی وابسته به آن نیز از بین خواهند رفت. با این وجود قبل از آنکه بتوان از حذف آنها را با قطعیت بیان کرد، لازم است وظایف آنان به روشنی تعریف و تفهیم شود.
1-2-2-11- وظایف قابلیت اطمینان
وسوسه نوشتن وظایف قابلیت اطمینان همیشه وجود دارد. در حقیقت، قابلیت اطمینان به خودی خود یک فعالیت نیست. یک انتظار کارایی است که در کلیه فعالیتهای دیگر گسترش مییابد. اهداف کلی قابلیت اطمینان میتواند مستند گردد. قابلیت اطمینان یک دارایی، در حقیقت از طریق برخورد مناسب با هر یک از مدهای خرابی که میتواند باعث توقف وظیفه گردد، مدیریت میشود.
1-3- تشریح وظایف[6]
کلیه تشریحات وظایف باید شامل یک فعل، یک مفعول و یک استاندارد کارایی باشد و در هر موردی که ممکن است باید کمیت آن مشخص گردد.
برای مثال شکل 1 پمپاژ پمپی را نشان میدهد که آب را از یک تانکر به تانکر دیگر پمپاژ میکند. ظرفیت معمول پمپ 1000 لیتر در دقیقه و آب با میزان حداکثر دبی 800 لیتر در دقیقه در حال تخلیه از تانکر است.
وظیفه اولیه این پمپ به این شکل توصیف میشود: پمپاژ آب از تانکر X به Y با دبی حداقل 800 لیتر در دقیقه. در اینجا ” پمپاژ کردن ” فعل، ” آب ” مفعول و ” از تانکر X به تانکر Y با حداقل دبی 800 لیتر در دقیقه” استاندارد کارایی، می باشد.
وضعیت فعالیت حفاظتی به بررسی ویژه نیاز دارد. این وظایف با استثنا عمل میکنند؛ به عبارت دیگر هنگامی که چیز دیگری درست عمل نکند؛ وضعیت وظیفه میبایست این حقیقت را نشان دهد. این امر معمولاً با ترکیب کلمه ” اگر” یا ” در مواقع ” به همراه خلاصه کوتاهی از شرایط و اتفاقاتی که حفاظت را فعال میکنند، انجام میشود. برای مثال وظیفه یک شیر اطمینان فشار ممکن است به شکل زیر تشریح شود: بتواند فشار را در بویلر[7] در صورتی که از 250 Psi فراتر رود، پایین بیاورد.
شکل 1: وظیفه یک پمپ
1-4- استانداردهای کارایی[8]
استانداردهای کارایی که در شرح وظایف گنجانیده شده اند میبایست در سطح عملکرد مطلوب مالک یا استفاده کنندگان دارایی یا سیستم در زمینه عملیاتی مربوطه باشند.
هر سیستمی که در محیط واقعی قرار گیرد دچار زوال و خرابی خواهد شد مگر آنکه اقداماتی برای مقابله با هر فرآیندی که باعث خرابی سیستم میشود، انجام گیرد.
برای مثال پمپهای گریز از مرکز[9] در معرض سایش پروانه هستند. پمپ اسید یا روغن روغنکاری را حرکت دهد و چه جنس پروانه از تیتانیوم باشد یا از فولاد ساخته شده باشد سایش اتفاق خواهد افتاد. تنها پرسشی که مطرح می شود این است که پروانه در چه صورتی به حدی از پوسیدگی و فرسودگی میرسد که دیگر قادر به پمپاژ مایع با حداقل میزان دبی مورد نیاز نمی باشد.
زمانی که کارایی یک دارایی به کمتر از مقدار مورد نظر استفاده کننده برسد، دارایی خراب شده است. برعکس آن، اگر کارایی دارایی بالاتر از مقدار حداقلی باقی بماند، دارایی به فعالیت خود ادامه خواهد داد.
همان طور که در این کتاب آمده است، استفاده کنندگان شامل مالکان دارایی، استفاده کنندگان و در مجموع جامعه می باشند.
مالکان در صورتی که داراییها بازده قابل قبولی از سرمایهگذاری انجام شده را برای آنها حاصل کند راضی خواهند شد.
مصرف کنندگان در صورتی که هر دارایی به انجام آنچه مورد انتظار آنها بر اساس یک استاندارد کارایی است ادامه دهد، راضی خواهند بود.
در نهایت جامعه در صورتی که دارایی در مسیرهایی که ایمنی یا محیط زیست را تهدید میکنند قرار نگیرند، راضی خواهد بود.
این اصل بدین معناست که اگر به دنبال این هستیم که دارایی به وظیفه خود در سطحی که مطلوب استفاده کننده باشد ادامه دهد، بنابراین هدف نگهداری و تعمیرات حصول اطمینان از ادامه انجام وظیفه دارایی در سطح حداقلی قابل قبول استفاده کنندگان می باشد. اگر میتوانستیم دارایی بسازیم که بتواند حداقل کارایی را بدون خرابی انجام دهد در آن صورت دارایی میتوانست به صورت مداوم بدون نیاز به نگهداری و تعمیرات به کار خود ادامه دهد.
به هر حال خرابی اجتناب ناپذیر است و رخ خواهد داد. این بدین معناست که هرگاه دارایی به کار گرفته میشود، باید بیش از حداقل استاندارد عملکرد مطلوب استفاده کننده را به انجام برساند. آنچه دارایی در این زمان انجام میدهد به عنوان ظرفیت اولیه آن شناخته میشود. شکل 2 ارتباط واقعی میان ظرفیت اولیه و عملکرد مطلوب را نشان میدهد.
کارایی را میتوان به دو روش مشخص کرد:
- عملکرد مطلوب (آنچه استفاده کنند از دارایی میخواهد تا تجهیز انجام دهد)
- توانایی اولیه (آنچه دارایی قادر به انجام آن است)
شکل 2: محدوده مجاز برای کاهش
محدوده کاهش باید به اندازه کافی بزرگ باشد تا مقدار معقول قابل استفاده بودن پیش از رسیدن به خرابی وظیفه ای را در نظر بگیرد؛ اما در حدی نباشد که سیستم مجدد طراحی گردد زیرا بسیار گران می باشد. در عمل این میزان در مورد بسیاری از اجزای تجهیز مناسب است، بنابراین معمولاً میتوان برنامههای نگهداری را بر اساس آن توسعه داد.
در هر حال اگر عملکرد مطلوب بالاتر از ظرفیت ساخت باشد، هیچ نگهداری و تعمیراتی نمیتواند عملکرد مطلوب را مقدور سازد که در این صورت دارایی غیر قابل نگهداری است.
تمام این موارد بدین معناست که به منظور تعیین اینکه آیا یک دارایی قابل نگهداری است یا خیر، لازم است هر دو نوع کارایی را بشناسیم: ظرفیت ساخت دارایی و حداقل عملکردی که مورد قبول استفاده کننده دارایی ، در زمینهای است که دارایی در آن در حال استفاده می باشد. این حداقل عملکرد ، استاندارد عملکردی است که میبایست در شرح وظیفه گنجانده شود.
برای مثال، ظرفیت اولیه پمپ شکل 1، 1000 لیتر در دقیقه است و میزان آبی که از تانکر خارج میشود 800 لیتر در دقیقه است. در اینجا تا زمانی که پمپ به پمپاژ آب به درون تانکر سریعتر از مقدار آبی که خارج میشود ادامه دهد، انتظارات استفاده کنندگان برآورده خواهد شد. در نتیجه وظیفه اولیه پمپ “پمپاژ آب از تانکر X به Y با سرعت حداقل 800 لیتر در دقیقه” تعریف میشود و نه “پمپاژ 1000 لیتر در دقیقه”.
توجه داشته باشید که اگر پمپی مشابه در شرایطی که خروجی تانکر 900 لیتر در دقیقه بود مورد استفاده قرار میگرفت در آن صورت وظیفه اولیه پمپ به صورت “پمپاژ آب از تانکر X به Y با سرعت حداقل 900 لیتر در دقیقه” تعریف میشد و برنامه نگهداری و تعمیرات در مقابل این انتظار عملکرد جدید تغییر میکرد.
توجه داشته باشید که استفاده کنندگان و تعمیر کاران اغلب دیدگاههای کاملاً متفاوتی درباره آنچه عملکرد مناسب در نظر گرفته میشود دارند. در نتیجه به منظور اجتناب از سوء تعبیر درباره آنچه خرابی وظیفه ای را شکل میدهد، حداقل استانداردهای عملکرد مطلوب باید به روشنی تفهیم شده و از سوی استفاده کنندگان و تعمیرکاران دارایی و نیز هر شخص دیگری که از رفتار دارایی منافع قانونی دارد پذیرفته شود.
استانداردهای کارایی در جایی که امکان پذیر است میبایست کمی باشند، چرا که استانداردهای کمی واضحتر و جامعتر از استانداردهای کیفی میباشند. در بعضی مواقع تنها میتوان از استانداردهای کیفی استفاده کرد. مثلاً هنگام کار با فعالیتهایی که مربوط به ظاهر میباشند. در چنین مواردی، باید دقت ویژهای به کار رود تا اطمینان حاصل گردد که استانداردهای کیفی از سوی استفاده کنندگان و تعمیرکاران دارایی، تفهیم و پذیرفته شده اند.
مرجع این متن کتاب “نگهداری و تعمیرات مبتنی بر قابلیت اطمینان بر اساس استانداردهای SAE JA 1011 و SAE JA 1012″ می باشد. این کتاب ترجمه استاندارد های SAE JA 1011 و SAE JA 1012” می باشد به همراه مثالهای تجربی که به عنوان مراجع اصلی نگهداری و تعمیرات مبتنی بر قابلیت اطمینان می باشند.
شما می توانید با ذکر نام منبع (سایت دانشنامه نت) و لینک سایت (www.mpedia.ir) این مطلب را باز نشر دهید.
[8] Performance Standards