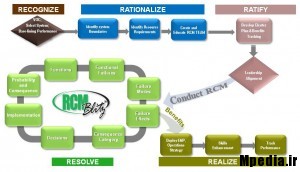
1– مدهای خرابی[1]
یک فرآیند RCM که مطابق با SAE JA 1011 باشد در مرحله بعد این پرسش را مطرح میکند: ” چه چیزی موجب خرابی وظیفه ای میشود (مدهای خرابی)؟ ” در این بخش به بحث درباره پنج مولفه کلیدی زیر میپردازیم که مربوط به مدهای خرابی می باشد.
i. تعریف مدهای خرابی
ii. مشخص کردن منظور عبارت ” احتمال منطقی “
iii. سطوح علت و معلول
iv. منابع اطلاعاتی
v. انواع مدهای خرابی
1-1- تعریف مدهای خرابی[2]
کلیه مدهای خرابی که منطقاً وقوع آنها محتمل است میبایست تعریف شوند.
در بخش قبل گفته شد که RCM میان وضعیت خرابی دارایی (خرابی وظیفه ای) و وقایعی که موجب وضعیت های خرابی میشوند (مدهای خرابی) تمایز قائل است. چرا که مشخص کردن دلایل خرابی تا زمانی که مشخص نکنیم منظور از کلمه ” خرابی” دقیقاً چه است، غیر ممکن است. فرآیند RCM خرابی های وظیفه ای را پیش از مدهای خرابی مشخص میکند. در شکل 3 روشی که معمولا از طریق آن، این امر مستند میشود برای وظیفه اولیه پمپی که در شکل 1 آمده است نشان داده شده است. شکل 3 که وظایف، خرابیهای وظیفه ای و مدهای خرابی یک دارایی را ذکر میکند، تقریباً کلیه مولفههای یک مد خرابی و تجزیه و تحلیل اثر (FMEA) آن را نشان میدهد. اثرات هر مد خرابی در گامهای بعدی ذکر شدهاند.
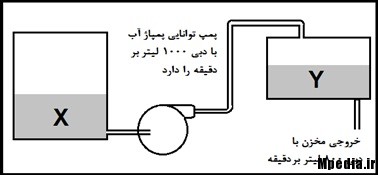
شکل 3 همچنین نشان میدهد که شرح یک مد خرابی حداقل میبایست دارای یک اسم و یک فعل باشد. این توصیف باید جزئیات کافی برای امکان انتخاب سیاست مدیریت خرابی مناسب را داشته باشد، اما نه آن قدر مشروح که مقدار زمان زیادی برای تجزیه و تحلیل خود فرآیند تلف شود.
افعالی که برای توصیف مد خرابی انتخاب میشود باید با دقت بالایی انتخاب شود چرا که تأثیر شدیدی بر فرآیند انتخاب سیاست مدیریت خرابی دارد. برای مثال، افعالی مانند “خرابی” یا “شکست” یا “سوء عملکرد” میبایست با احتیاط استفاده شوند؛ زیرا درباره آنچه ممکن است راه حل مناسب مدیریت مد خرابی باشد ، نشانههای کمی در اختیار میگذارند و یا اصلاً نشانهای به ما نمیدهند. استفاده از افعال خاصتر انتخاب از میان طیف گسترده گزینههای مدیریت خرابی را میسر میسازد.
برای مثال مد خرابی 1A4 در شکل 3 ممکن است به صورت ” خرابی کوپلینگ ” تعبیر شده باشد. چنین عبارتی هیچ سر نخی درباره آنچه ممکن است برای پیشبینی یا جلوگیری از مد خرابی انجام شود به ما نمیدهد. اگر بگوییم پیچهای اتصال شل میشود یا مراکز اتصال به دلیل پوسیدگی قطع میشود آن وقت تشخیص یک عمل کنش گرایانه بسیار آسانتر خواهد بود.
شکل 3: مدهای خرابی پمپ
برای شیرها، کلیدها و تجهیزات مشابه، توصیف مد خرابی میبایست مشخص کند که دلیل از دست دادن وظیفه ، عدم کارکرد تجهیز در باز کردن بوده یا در عدم کارکرد تجهیز در بستن.
عبارت ” شیر بر اثر گرفتگی بسته شده ” بیشتر از عبارت ” شیر دچار گرفتگی شده ” به ما اطلاعات میدهد. علاوه بر این، هدف از تعریف مدهای خرابی، تشخیص علت خرابی وظیفه ای است تا راهی برای پیشبینی یا پیشگیری از آن پیدا شود. در نتیجه ممکن است گاهی لازم باشد این مرحله اضافی را انجام دهیم، مانند مورد ” شیر بر اثر گرفتگی بسته شده که به خاطر زنگ زدگی پیچ آن می باشد “. در این زمینه، استفاده از کلمه ” زنگ زدگی ” نشان میدهد که شاید بهتر باشد مدیریت خرابی را بر روی تلاش برای شناسایی و کنترل زنگ زدگی متمرکز کنیم.
1-2- مشخص کردن معنای عبارت احتمال منطقی[3]
روش تصمیم گیری درباره اینکه چه دلایلی باعث رخداد یک مد خرابی می شوند، باید برای مالک یا استفاده کننده از دارایی قابل قبول باشد.
در بخش قبل بیان شد که ، کلیه مدهای خرابی که از نظر منطقی احتمال دارد موجب رخداد هرگونه خرابی وظیفه ای شوند، میبایست مشخص گردند. احتمال به معنی رسیدن به معقولیت می باشد ، زمانی که توسط افراد آگاه و آموزش دیده بکار برده میشود. در این استاندارد اغلب به جای ” منطقی ” از عبارت ” معتبر ” استفاده میشود.
اگر افرادی که برای استفاده از RCM آموزش دیدهاند و کسانی که در زمینه عملیاتی دارایی آگاهی دارند توافق کنند که احتمال وقوع یک مد خرابی خاص به شکل قابل توجهی بالا میباشد به نحوی که نیاز به تجزیه و به تحلیل آینده آن دارایی بوجود آید، در آن صورت مد خرابی میبایست ذکر شود.
گاهی تصمیم گیری در مورد اینکه آیا مد خرابی میبایست ذکر شود یا خیر در عمل بسیار دشوار است. این مسئله هم به احتمال وقوع و هم به سطح جزئیات مورد استفاده در توصیف مدهای خرابی مرتبط است. تعداد کم مدهای خرابی یا جزئیات کم گاهی به تحلیل ظاهری و گاهی تحلیل خطرناک منجر میشود. تعداد مدهای زیاد با جزئیات فراوان باعث میشود تا کل فرآیند RCM بیش از آنچه لازم است به طول انجامد. در موارد سخت این امر میتواند باعث شود که فرآیند دو یا حتی سه برابر بیش از مدت زمان لازم طول بکشد ،پدیده ای که با عنوان تحلیل ناقص شناخته میشود و نیز ممکن است منجر به برنامههای نگهداری بسیار طاقت فرسا گردد. در مواقعی که ممکن است درباره آنچه مستدل می باشد مخالفت یا شک وجود داشته باشد، تصمیم نهایی میبایست از سوی سازمان مالک یا استفاده کننده دارایی اخذ گردد تا در صورت وقوع خرابی، سازمان مالک یا استفاده کننده مسئول نهایی عواقب مد خرابی باشد. توجه داشته باشید که تصمیم به ذکر یک مد خرابی میبایست با در نظر گرفتن عواقب آن انجام گردد. اگر احتمال برود که عواقب بسیار شدید باشند در آن صورت باید مدهای خرابی با احتمال کمتر لیست گردیده و مورد تجزیه و تحلیل بیشتر قرار گیرند.
برای مثال اگر پمپی که در شکل 3 توصیف شد در یک کارخانه مواد غذایی یا کارخانه مونتاژ خودرو نصب میشد مد خرابی (شکستگی پوسته بدلیل سقوط شی از آسمان) بدلیل اینکه کاملاً غیر محتمل است فورا منتفی خواهد شد با این حال اگر پمپ مشابه ای به عنوان پمپ خنک کننده اولیه در یک راکتور هستهای در نیروگاه برق تجاری باشد، این مد خرابی بیشتر احتمال دارد جدی گرفته شود حتی اگر همچنان غیر محتمل باشد. استراتژی های مدیریت خرابی مناسب ممکن است هواپیما را از پرواز بر روی کارخانجات منع کند، یا سقفی را طراحی کند که بتواند در برابر سقوط هواپیما مقاومت کند این مسئله تنها یک حدس و گمان ساده نیست و البته معمولا هر دو سیاست در نیروگاههای هسته ای در نظر گرفته میشوند.
1-3- سطوح علت[4]
مدهای خرابی میبایست در سطحی از علت مشخص گردند که امکان تعیین سیاست مدیریت خرابی مناسب ممکن باشد.
در بخش قبل گفته شد که مدهای خرابی میبایست با جزئیات کافی به منظور انتخاب سیاست مدیریت خرابی مناسب شرح داده شوند، اما نه آن قدر مفصل که مقدار زمان زیادی را در خود فرایند تجزیه و تحلیل تلف شود.
مقدار جزئیاتی که مدهای خرابی باید در آن سطح تشریح گردند در شکل 4 نشان داده شده است که بر اساس پمپی است که وظایف و خرابیهای وظیفه ای آن در شکل 3 شرح داده شد. شکل 4 برخی مدهای خرابی را که ممکن است باعث خرابی وظیفه ای شوند مانند عدم توانایی در انتقال آب را نشان میدهد. در این مثال این مدهای خرابی در 7 مرحله در نظر گرفته میشود که با خرابی پمپ به عنوان یک مجموعه کلی آغاز میشود.
اولین نکتهای که در این مثال مشخص میشود ارتباط میان سطح جزئیات و تعداد مدهای خرابی ذکر شده است. این مثال نشان میدهد که هر چه کنکاش در یک FMEA بیشتر باشد تعداد مدهای خرابی که میتوان ذکر کرد بیشتر میشود. برای مثال، 3 مد خرابی برای پمپ در مرحله 3 شکل 4 آمده است در حالی که در مرحله 6 تعداد آن 20 مورد می باشد.
نکته دیگری که از شکل 4 بدست میآید علل ریشهای است که در زیر بحث میشود.
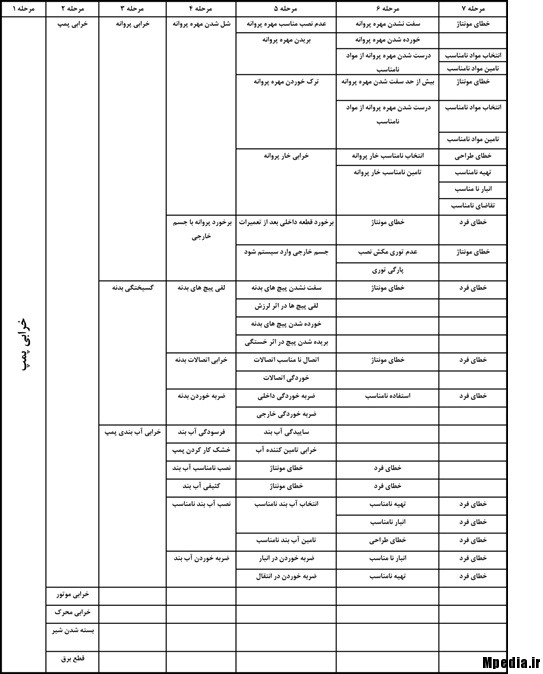
شکل 4: مدهای خرابی در سطوح مختلفی از جزییات
1-3-1- علل ریشهای
اصطلاح علل ریشهای اغلب در ارتباط با تجزیه و تحلیل خرابیها مورد استفاده قرار میگیرد و نشان میدهد که تنها در صورتی میتوان به یک علت قطعی و نهایی دست یافت که به قدر کافی کنکاش کرده باشیم. در حقیقت انجام این امر نه تنها بسیار دشوار است بلکه معمولا غیر ضروری نیز می باشد.
برای مثال در شکل 4، مد خرابی “مهره پروانه شل شده است” در سطح 4 ذکر شده که به ترتیب به خاطر “ترک خوردن مهره پروانه” در مرحله 5 ایجاد شده است. اگر یک مرحله پایینتر برویم این ترک ممکن است به دلیل “بیش از حد محکم شدن مهره پروانه” در مرحله 6 ایجاد شده باشد که ممکن است به دلیل خطا در مونتاژ در مرحله 7 اتفاق افتاده باشد. خطا در مونتاژ ممکن است به این دلیل اتفاق افتاده باشد که حواس تکنیسین پرت شده است (مرحله 8). تکنسین ممکن است به دلیل بیماری فرزندش تمرکز کافی نداشته باشد (مرحله 9). این مد خرابی ممکن است به این دلیل اتفاق افتاده باشد که کودک در رستوران غذای نامناسبی خورده است (مرحله 10).
واضح است که این فرآیند کنکاش تقریبا میتواند برای همیشه ادامه یابد ، فراتر از حدی که سازمان مسئول عملیات دارایی و نگهداری وتعمیرات دارایی، کنترلی بر مدهای خرابی داشته باشد. به همین خاطر است که SAE JA 1011 برای فرآیند RCM نیازمند است که مدهای خرابی را در سطحی از عوامل مشخص کند که تشخیص سیاست مدیریت خرابی مناسب را امکان پذیر سازد. این مرحله در مدهای خرابی مختلف، متغیر خواهد بود. ممکن است برخی مدهای خرابی در مرحله 3 مشخص ، برخی دیگر در مرحله 5 و مابقی در مراحل دیگر مشخص گردند.
توجه داشته باشید که مدهای خرابی که در شکل 4 نشان داده شدهاند ممکن است در زمینهای دیگر از آنچه برای شکل 4 استفاده شده از نظر منطقی محتمل نباشند. در آن صورت هیچ دلیلی برای اشاره به آنها وجود ندارد و برعکس آن مدهای خرابی که در شکل 4 نشان داده نشدهاند اما از نظر منطقی احتمال وقوع آنها در آن زمینه وجود دارد، ممکن است به لیست اضافه شوند. همچنین در نظر داشته باشید که مدهای خرابی که در شکل 4 آمدهاند تنها در مورد خرابی وظیفه ای و عدم توانایی در انتقال آب است. شکل 4 مدهای خرابی را که موجب خرابی های وظیفه ای دیگر مانند نبود حفاظت و یا نبود کنترل است را نشان نمیدهد.
1-4- منابع اطلاعات در مورد مدهای خرابی[5]
فهرست مدهای خرابی میبایست شامل مدهای خرابی باشد که قبلا رخ دادهاند ، مدهای خرابی که در حال حاضر با برنامههای نگهداری و تعمیرات موجود جلوگیری می شوند و نیز مدهای خرابی که هنوز رخ ندادهاند اما گمان میرود که از نظر منطقی در آن زمینه محتمل باشند.
مدهای خرابی که قبلا در دارایی یکسان یا مشابه ای رخ دادهاند آشکارترین مواردی هستند که در فهرست مدهای خرابی قرار میگیرند، مگر آنکه این مدهای خرابی به گونهای تغییر کنند که امکان وقوع مجدد آنها از بین برود. منابع اطلاعاتی این مدهای خرابی شامل افرادی است که دارایی را به خوبی میشناسند و نیز سابقه فنی و بانک اطلاعاتی دارند (اپراتورها، تعمیرکاران، فروشندگان تجهیزات یا استفاده کنندگان تجهیزات مشابه).
مدهای خرابی که موضوع روتینهای نگهداری و تعمیرات پیش اقدامانه موجود میباشند، میبایست در فهرست مدهای خرابی گنجانده شوند. یکی از راههای اطمینان از اینکه هیچ یک از این مدهای خرابی نادیده گرفته نشده این است که برنامههای نگهداری موجود را در مورد داراییهای یکسان و یا مشابه بررسی کرده و این سوال را مطرح کنیم که ” در صورت انجام نشدن این کار چه مدهای خرابی اتفاق میافتد؟ ” اگر چه برنامههای موجود میبایست تنها پس از آن که ادامه فرآیند تجزیه و تحلیل RCM تکمیل شد به عنوان یک بررسی پایانی مورد مطالعه قرار گیرند تا احتمال تداوم وضع موجود کاهش یابد.
در نهایت فهرست مدهای خرابی میبایست شامل مدهای خرابی که هنوز به وقوع نپیوسته اما در زمینه مورد نظر امکان وقوع دارد نیز باشد. تشخیص و تصمیم درباره چگونگی مواجهه با مدهای خرابی که هنوز رخ نداده از ویژگیهای ضروری کلی مدیریت کنش گرایانه و از ویژگیهای خاص مدیریت ریسک است و نیز یکی از چالش برانگیزترین جنبههای چشمانداز RCM است، چرا که مهارت و دانش افراد در این امر از اهمیت بالایی برخوردار است.
1-5- انواع مدهای خرابی[6]
فهرست مدهای خرابی میبایست شامل هر رویداد یا فرآیندی باشد که احتمال دارد باعث خرابی وظیفه ای شامل نقص تجهیز، نقص طراحی و خطای انسانی ، خواه توسط اپراتورها یا تعمیرکاران رخ دهد ، باشد. مگر آنکه خطای انسانی به وسیله فرآیندهای تحلیلی جدا از RCM نشان داده شده باشد.
خرابی هنگامی رخ میدهد که ظرفیت یک دارایی برای شروع بالاتر از عملکرد مطلوب باشد اما بعد از آنکه دارایی به کار گرفته میشود به پایینتر از عملکرد مطلوب میرسد. این مسئله شامل کلیه اشکال ساییدگی و پارگی مانند فرسودگی، خوردگی، سایش ، تبخیر، تخریب (به ویژه عایق، روغن و …) و غیره میشود. البته این مدهای خرابی میبایست در فهرستی از مدهای خرابی که گمان میرود از نظر منطقی متحمل هستند و در مناسبترین سطح ممکن تشریح شوند.
در برخی موارد، طراحی یک دارایی یا تنظیمات یک سیستم ممکن است آن را در انجام کامل الزامات عملیاتی در زمینه موارد انتظار، ناتوان کند. اگر چنین نواقصی بر تجهیزات موجود تاثیر گذار شناخته شوند و یا اگر در مورد تجهیزات جدید گمان رود که فرآیندهای مدیریت طراحی و ساخت موجود قادر به تشخیص و رفع این نواقص نمیباشند، در آن صورت این مدهای خرابی میبایست به گونهای ذکر شوند که بتوان استراتژی های مدیریت خرابی مناسب را در آنالیزهای بعدی تعریف کرد.
بسیاری از خرابی های وظیفه ای هنگامی رخ میدهند که فشار وارد بر یک دارایی بیش از توانایی تحمل آن افزایش یابد. در عمل این افزایش فشار اغلب توسط انسان انجام میشود. مطالعات انجام شده درباره این موضوع چنین خطاهای انسانی را به انواع مختلفی دسته بندی میکند. اگر چه در زمینه دارایی فیزیکی این خطاها به یکی از دستههای زیر مربوط میشود:
الف. کاربری نادرست: این مسئله معمولا به دو صورت می باشد.صورت اول پایدار، اغلب عمدی و بار اضافی است. برای نمونه میتوان ماشینی را مثال زد که در سطح عملکردی کار میکند که برابر با ظرفیت اولیه یا فراتر از آن است؛ مانند موتور خودرویی که به شکل مداوم با RPM بالایی کار میکند و موجب میشود تا به صورت نابهنگامی از کار بی افتد. دومین صورت، ناگهانی، معمولا غیر عمدی و بار اضافی است. مانند خودرویی که در هنگام حرکت به جلو در دنده معکوس قرار میگیرد و به جعبه دنده صدمه وارد میشود.
ب. مونتاژ معیوب: مثلا اگر مکانیکی ابزار را در جعبه دنده جا بگذارد یا برق کار سیمهای کلیدی را اشتباه وصل کند.
ج. صدمات خارجی: برای مثال پمپی که به وسیله لیفتراک پرس شده است.
اگر گمان میرود که چنین افزایشهایی در فشار وارده در زمینه مورد نظر از نظر منطقی محتمل میباشند و اگر در حال حاضر تحت فرآیند تحلیلی دیگری نمیباشند، میبایست در فهرست مدهای خرابی آورده شوند تا بتوان استراتژی های مدیریت خرابی مناسب را تعیین کرد.
شما می توانید با ذکر نام منبع (سایت دانشنامه نت) و لینک سایت (www.mpedia.ir) این مطلب را باز نشر دهید.
[2] Identifying Failure Modes
[3] Establishing what is Meant By “Reasonably Likely”
[5] Sources of Information about Failure Modes
[6] Types of Failure Modes